Fast heat-up with consequences
In practice, refractory lining repairs are frequently carried out under considerable time pressure. Every day earlier that the repaired unit can go back on line, increases productivity for the owner/operator. This time pressure can lead to a situation where in some cases the heat-up requirements necessary for conventional cement-bonded refractory concrete cannot be fulfilled.
As known, excessively fast heating up of cement-bonded concretes frequently results in damage (cracks, spalling, explosion).
Risk-free application
Therefore, Refratechnik aimed at developing a range of refractory castables that are insensitive to rapid heating.
After the Nanobond products have been heated to a temperature of 150 °C, they are free of water. Subsequently, the heating rate is only limited by material stresses due to thermal expansion.
The solution lies in products based on the Nanobond technology, on which you can rely – also under the extreme conditions encountered in practice.
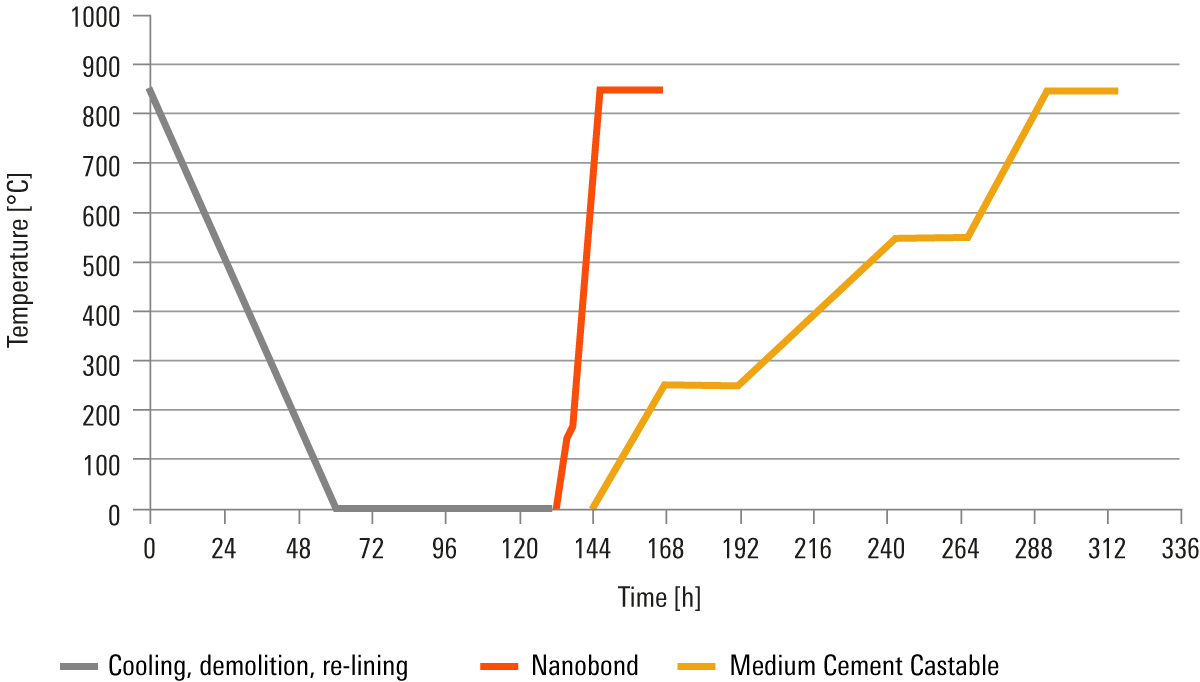
Up to 85% faster heating up
As an example, the flowchart for the repair of an aluminium melting furnace shows the reduction of heat-up time from 6 days when using cement-bonded materials (here: medium cement castable) down to less than 1 day when using Nanobond products. Moreover, Nanobond-based castables can be heated up as soon as they have cured and the formwork has been removed, without having to wait for the formation of the hydrated cement phases, which can take up to 24 hours with conventional concretes. By adding accelerators, the actual curing time can be influenced individually.
Even more time can be saved by using REFRAJETCRETE® shotcrete products based on the Nanobond technology. All delays due to installation/removal of formwork are eliminated, and no curing times must be taken into account. Heating up can start as soon as the material has been shotcreted.
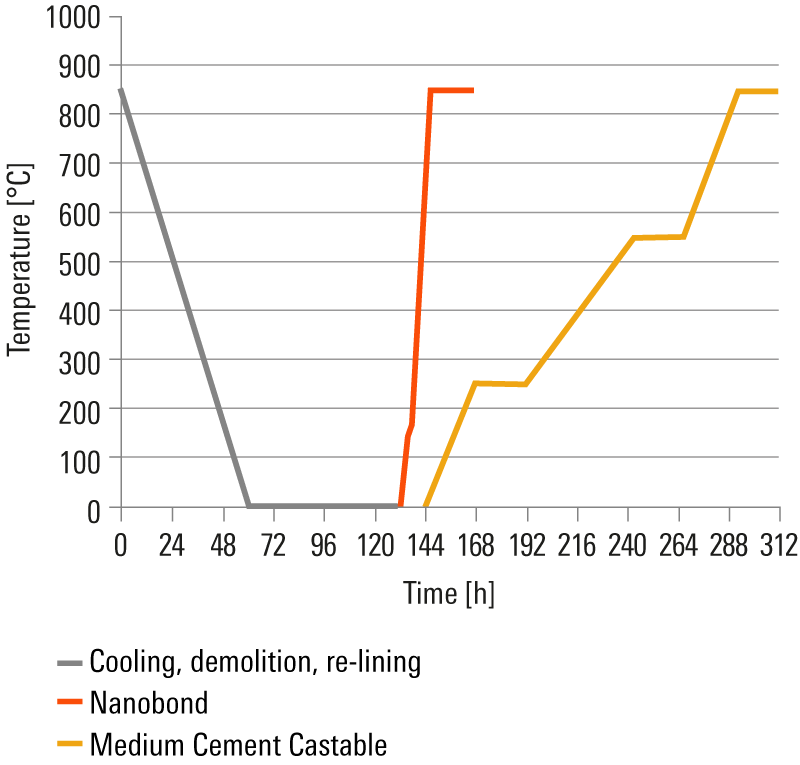
Perfect adherence
Nanobond products adhere perfectly to the surfaces of other refractory materials. Hereby, the surface temperature only plays a subordinate role.
Practice has shown that lining work can be carried out on surfaces up to 1000 °C without problems. This outstanding property makes Nanobond products an ideally suited repair material.
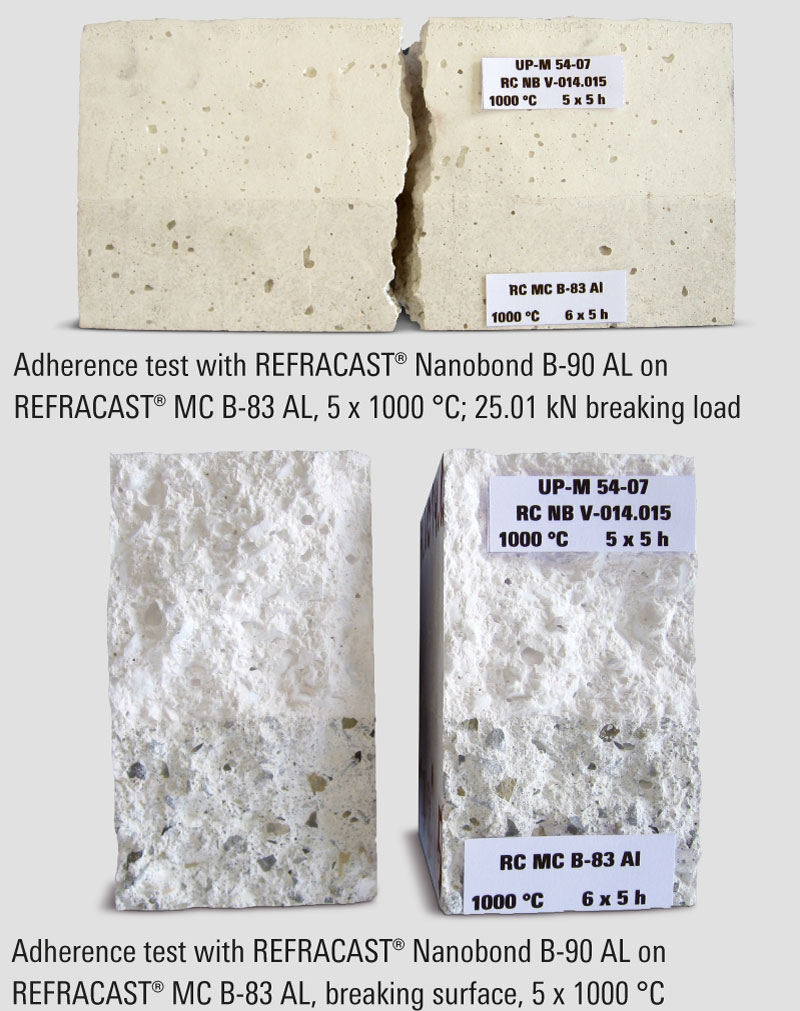
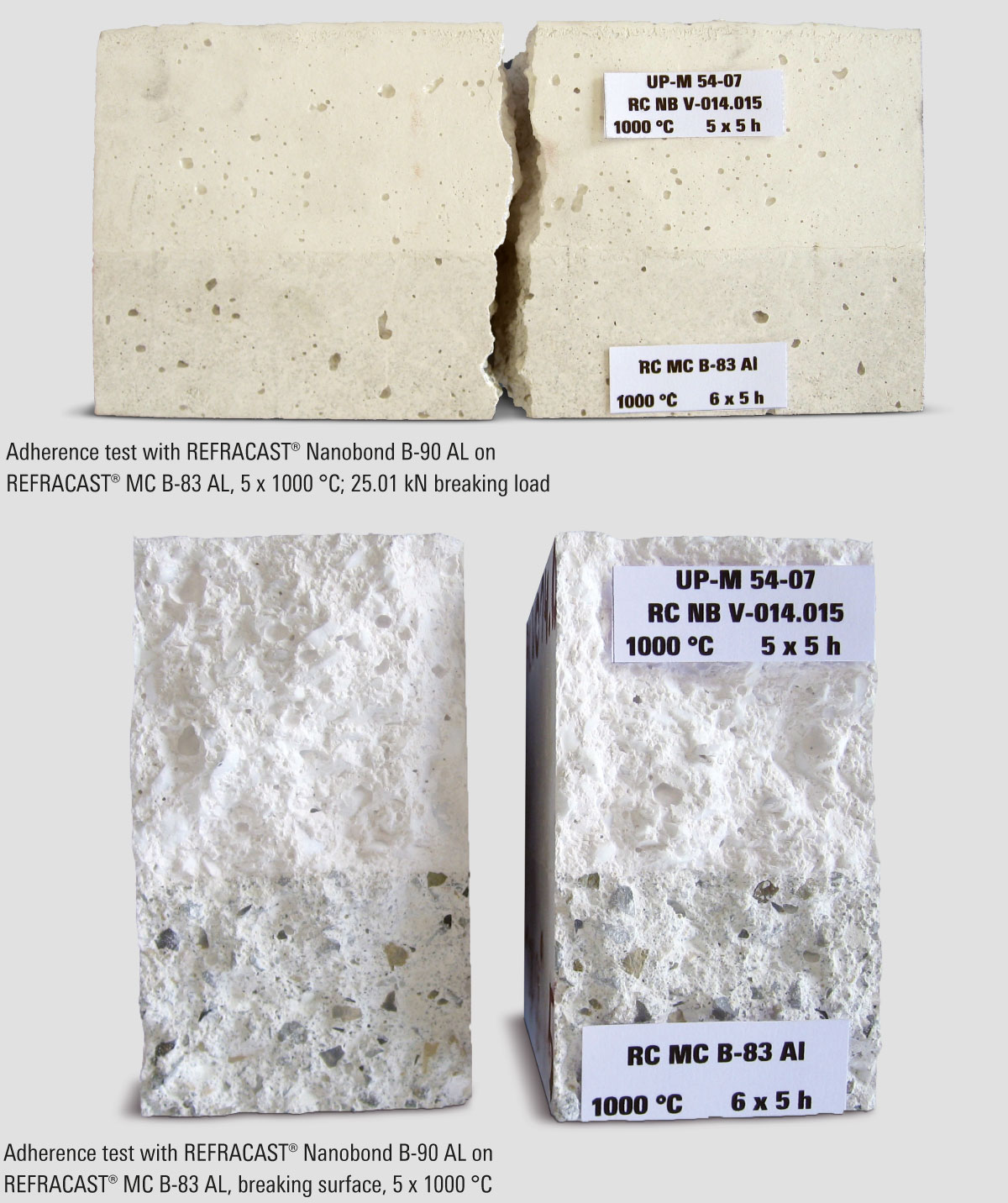
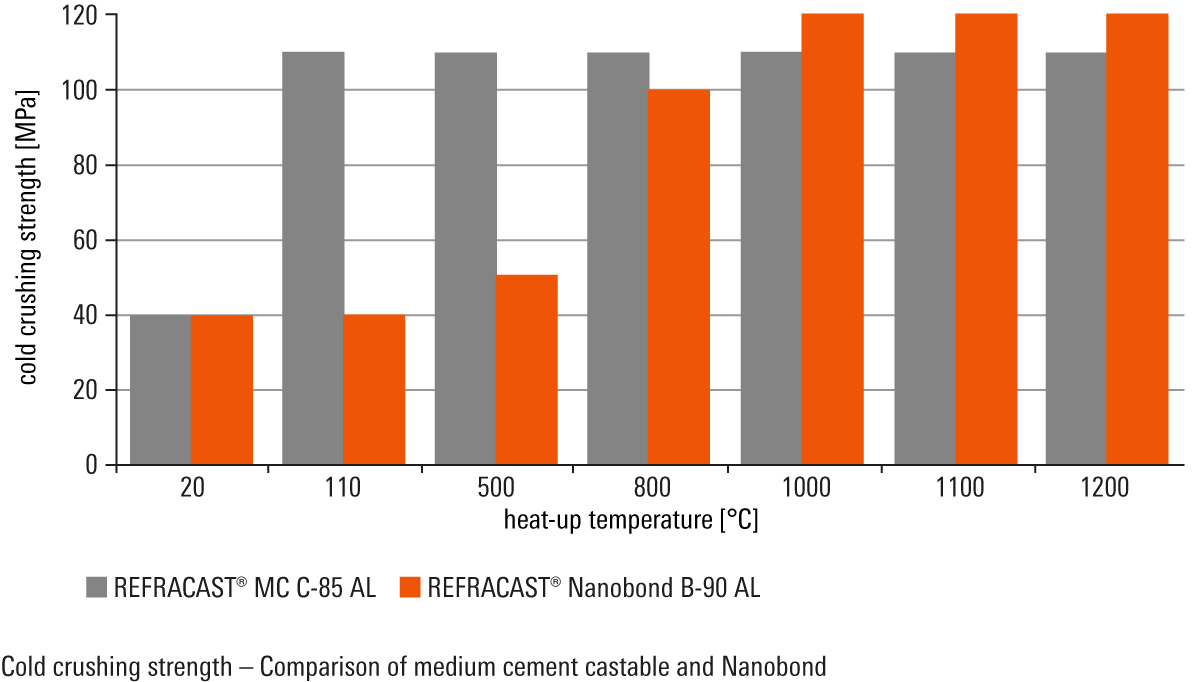
High strength
After reaching a temperature of 800 °C, Nanobond products exhibit similar values for strength as cement-bonded materials.
Due to the hydrated cement phases that occur in the curing process, cement-bonded materials exhibit very good strength values already while curing, and these are not increased significantly during heat-up. Initially, the strength of Nanobond-based materials is lower, but due to the formation of Nanobond-specific bonds during heat-up, strength is increased considerably.
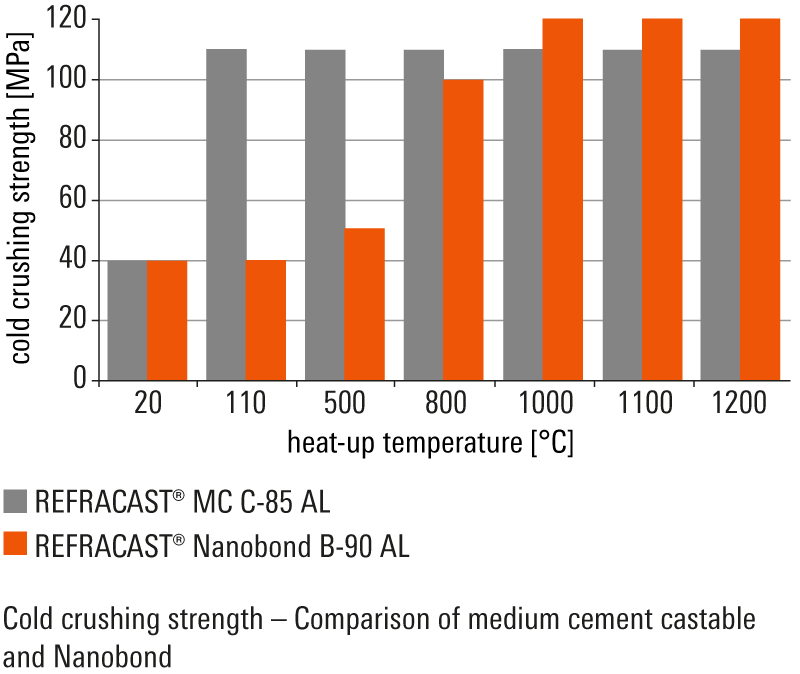
Multiple application options
Thanks to their outstanding properties, Nanobond-based products are equally suitable for repair work and as material for installing complete linings. If you want to get your system up and running as quickly and as safely as possible, products using Nanobond technology are the right choice.
Advantages at a glance
- Heat-up rates between 50 and 100 °C/h possible, with enormous cost savings for the owner/operator
- Excellent adherence to other materials
- Easy workability of the products
- No health hazard (as opposed to other 2-component products)
- High refractoriness
- Long storage life up to 12 months